How we built our Robotic Bubble Tea Station
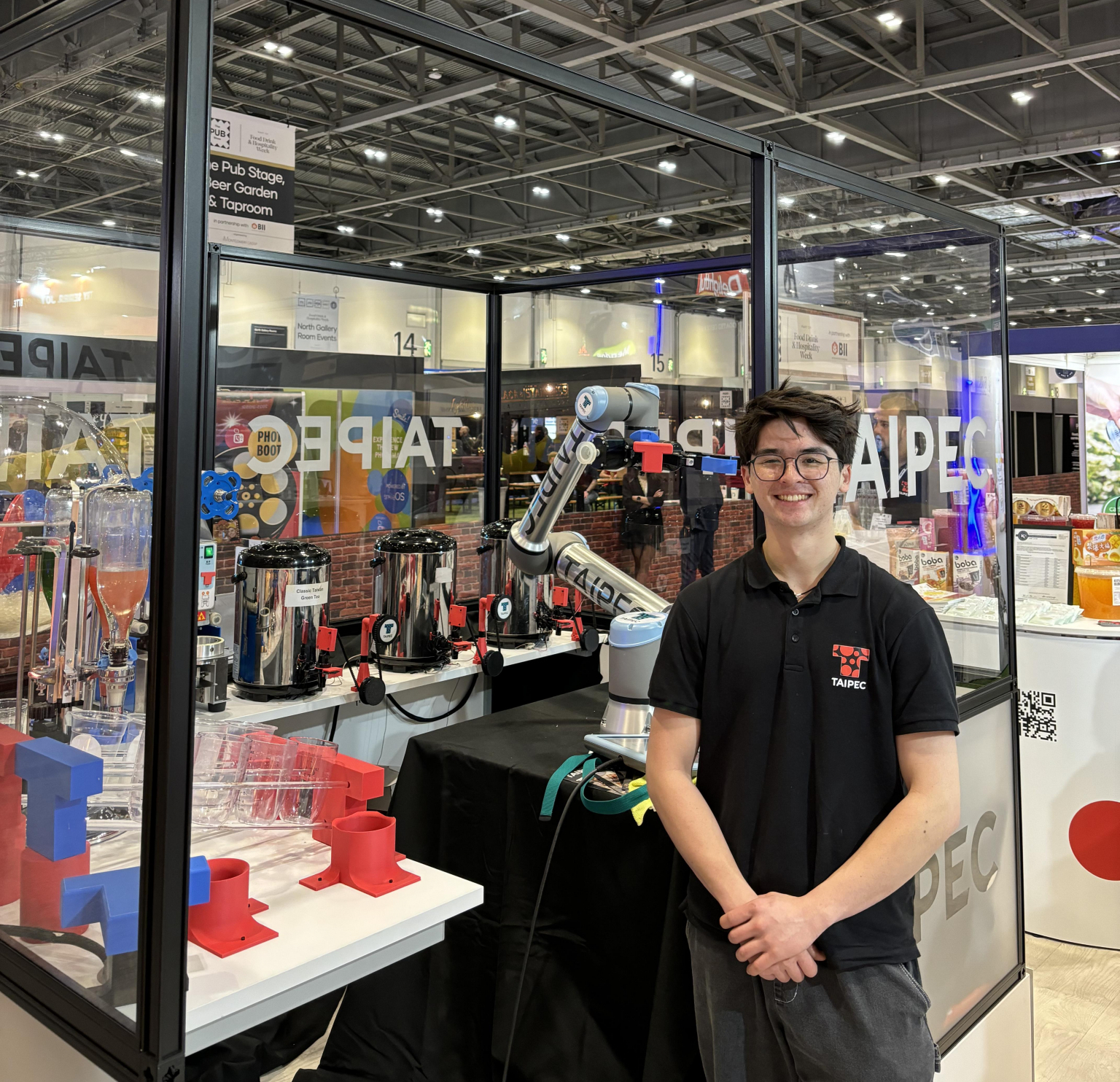
This post is written by our in-house R&D engineer Thomas Hodges.
Robotic Bubble Tea Station — The Brief
The idea of producing an automated drinks station is nothing new, but specifically an automated Bubble Tea station has its own problems and remained largely unsolved. The key issue is that you are dealing with a mix of liquids and solids, and these solids also stick to each other when stored outside their normal liquids.
Given Taipec's strong culture of innovation and its past collaborations with the University of Cambridge, University of Bath, and the Royal Academy of Engineering, and its commitment to developing staff, I could not help but be attracted to this challenge.
The Timeline
Our target was the International Food and Drinks Exhibition which ran between 25-27th March 2024 at Excel London.
Having joined Taipec in August 2023, I had to ask first: is this achievable? What do I have to learn? What's the timeline like? When setting out I knew I had to meticulously plan for and schedule down to the day, the goals I needed to hit and the skills I needed to gain.
For such a complex system like this, what I learned from doing this is that my timeline worked the most effectively when not meticulously planning every minute detail, but instead only capturing key project milestones and deadlines I needed to hit first, then planning for each deadline individually as they come. Although this may not work for everyone, I found that this way allowed me to remain flexible to tackle each challenge with a fresh mindset and more knowledge than if I planned from the start.
The challenges along the way
I tackled the most challenging programming problems collaboratively my software engineer colleague Eamonn Rolander. While he was working here over the summer, he wrote the core code base for working with the robotic arm and conceptualised the communication network that I would go on to completely flesh out and implement. This laid the groundwork for a lot of the more complicated communication with the two RaspberryPi wired into motors and our cup sealing machine as well. Having these tasks out the way early led me to be able to focus on more laborious and time-consuming parts of the project later on.
An aspect which was high workload was the amount of 3D modelling and 3D printing required. My strengths lie in 3D modelling, which proved invaluable in such a time-constrained environment. Although I considered using designs which involved complex organic forms, I opted for rectilinear bodies and shapes due to the time constraints and being more in line with Taipec logo’s design style.
I ran Finite Element Modelling on various plastic materials such as PLA (polylactic acid) and PC (polycarbonate) to determine the forces on the material. This would dictate how thick and how strong to print these parts. There is the additional complexity that they do not behave isotropically, meaning that their strength and stiffness depend on the direction of loading and resistance to that load.
Leading up to the exhibition, we encountered significant setbacks, with the primary one being a 3D printer bottleneck. Given many components would take 3-4 days to print, and often failing a couple of days into the process, we invested in two additional printers, as the time saved fixing faulty prints greatly outweighed the cost of the extra machinery.
The most troublesome aspect of the 3d printing was the popping boba dispenser, whose parts repeatedly failed to print despite numerous attempts, consuming significant amounts of PLA filament and time. As the Exhibition date drew closer, we had considered outsourcing to a 3D printing service as a backup. However, this did not have to be used, as over time through trial and error researching I found the perfect settings to match the material used which tested my resilience in attempting multiple solutions until success is achieved.
Another unforeseen challenge arose during the “wet-runs”, where the extra weight of all the liquids now posed a challenge for the plastic attachments on the robot grippers. Addressing this was easy though, incorporating a rubber sheet to enhance grip, however what I now realise is that from the start “wet-runs” should have been used constantly rather than when we were approaching the finish line.
Dress Rehearsals
Additionally, facing the task of setting up and recalibrating the robot within a two-day timeframe was a daunting challenge. With limited time and resources, I focused on meticulously measuring and ensuring consistency in the setup, then programming the robot from the start to ensure accuracy within movements, as the robot needs to be precise within 1 to 2 millimetres. This experience again demonstrated the importance of foresight in anticipating challenges and allocating time efficiently to address them.
In the end, the groundwork laid before the exhibition in anticipation of the transport of the space and quick set up led to the successful operation of the robot during the exhibition.
Impact
Throughout the show, several people had started to post onto Tiktok and Instagram. We posted our own video below.
View this post on Instagram
Looking back with all the knowledge I have now, it is safe to say that I could have navigated through the roadblocks and difficulties more smoothly, but the ‘wow factor' this robot had on the exhibition was immense. There were times that a large crowd had congregated around the robot arm's enclosure and caused pedestrian traffic to stall. We were certainly the talk of the show and we are very proud of it.